Improving Quality Management Capacity with Process Mapping
6 octobre 2017
G.Tyrrell Clinical Lead Pharmacist Surgery and Aseptic Services, Royal Glamorgan Hospital, UK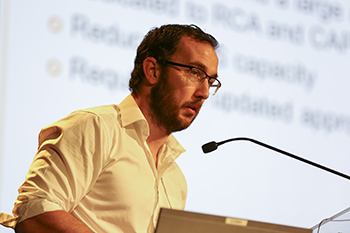
Essential to effective application of quality management systems (QMS) is the reporting of deviations from set service outcomes. Whilst identification and immediate resolution (Correction Actions) of these deviations indicates the presence of acceptable checking and reporting standards, the occurrence of such a deviation in the first place can suggest a failure in the underlying processes. An effective QMS framework should allow for robust investigation of deviations from accepted standards via root cause analysis (RCA) techniques. The aim is to identify CAPA actions to engineer the potential for future failure out of the system.
Current methods of investigation and resolution of deviations can be time-consuming and potentially ineffective. Consequently, the Cwm Taf UHB Aseptic Service developed process map tools to make the investigative process consistent and efficient. These tools were developed and introduced into the unit QMS in January 2015 and this study assesses the impact on QMS capacity.
By comparing the average time of incident closeout pre-and post-introduction of process map RCA tools the results showed that incidents durations were reduced from 18.3 days to 11.2 days. The results highlight that process map tools of common systems within GMP allow more efficient and consistent investigation of deviations which are applicable to many different systems within the service.