Analyse Lean d’une unité de production des chimiothérapies
7 octobre 2016
L. Carrez Pharmacy, Geneva University Hospitals, Geneva, Switzerland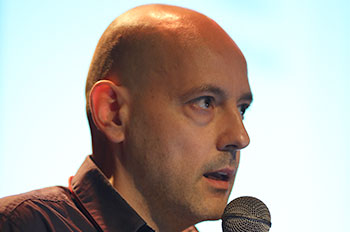
Les Hôpitaux Universitaires de Genève (HUG) ont centralisé leur production de chimiothérapies à la pharmacie depuis 2002. La pharmacie produit tous les traitements d’anticancéreux reconnus comme carcinogènes, mutagènes et toxiques pour la reproduction ainsi que tous les anticorps monoclonaux conjugués avec une molécule cytotoxique. Les demandes de production n’ont cessée de progresser pour atteindre 12554 chimiothérapies en 2006 et 16402 au cours de l’année 2014, soit une augmentation de la demande de 31% sur 8 ans.
Pour faire face à cette augmentation constante dans un contexte de maîtrise des coûts de la santé ne permettant pas le financement de ressources humaines supplémentaires, la pharmacie a dû repenser sa stratégie organisationnelle. Elle a automatisé une partie de la fabrication, entamé le développement de productions de série de chimiothérapies à dose fixe (« dose-banding ») et revu ses processus de production à travers une méthode Lean.
Le Lean est une philosophie de management de production développé dans l’industrie automobile et pour la première fois chez Toyota dans les années 50. Elle est basée sur l’élimination des gaspillages, Muda (surproduction, attentes, transports, étapes inutiles, stocks, mouvements inutiles, corrections/retouches), des excès, Muri (surcharges de travail, sur-stockage), et de la variabilité, Mura (fluctuation d’activité, de qualité et variabilité des processus). Comme toute méthode qualité, elle vise, par l’amélioration continue, à l’augmentation de la qualité et de la sécurité des produits, à l’efficience de production et à la satisfaction du client. L’originalité de la méthode vient de la forte implication du personnel à tous les niveaux et du fait que les propositions d’amélioration proviennent des collaborateurs, qui se trouvent au plus près de l’opérationnel.
La mise en œuvre de la méthode repose sur un processus en 5 étapes :
- La première étape consiste en la rédaction d’une charte impliquant l’ensemble du personnel et définissant les objectifs à atteindre, la cartographie du système de production et la définition des différentes familles (grand types de processus).
- La deuxième étape est la mesure du temps de chaque étape des processus.
- La troisième étape est l’analyse des temps et l’identification des étapes à grandes et faibles valeurs ajoutées.
- La quatrième étape est la recherche de l’amélioration de l’efficience des processus avec l’élimination ou la réduction des étapes à faibles valeurs ajoutées et l’utilisation d’outils organisationnels :
- 5S
- Seiri : trier l’utile de l’inutile et débarrasser le poste de travail
- Seiton : ranger chaque chose à sa place
- Seiso : nettoyer chaque jour
- Seiketsu : standardiser les règles de rangement et de nettoyage
- Shitsuke : maintenir la discipline d’ordre et de propreté
- Management visuel par une signalisation claire et efficace
- Standardisation du travail
- Réduction des temps de préparations avant une opération (SMED single minute exchange of die)
- Lissage de la charge de travail (heijunka)
- Production en flux tiré (JIT just in time)
- Définition d’une limite de production (Kanban)
- Définition d’un rythme de production (Takt time)
- Utilisation de détrompeur (Poka-Yoke)
- Organisation des déplacements (cellule en U)
- Management organisationnel (Obeya)
- La cinquième étape est une étape de contrôle pour mesurer l’amélioration.
Après avoir été oublié, le Lean connaît un nouvel essor depuis 2010 notamment dans le domaine de la santé. Elle a ses adeptes et ses opposants. On lui reproche souvent de pousser au taylorisme et d’être utilisée que dans un objectif de gain de productivité au dépend de l’être humain. Mais il s’agit souvent d’un détournement de l’utilisation de la méthode en opposition avec la philosophie prônée par le Lean.
Nous vous proposons de voir un exemple d’application de la méthode Lean à travers la réorganisation d’une unité de chimiothérapie. L’objectif n’étant pas la recherche d’un gain économique mais d’un gain d’efficience des processus et de sécurité des préparations en améliorant les conditions de travail des opérateurs, notamment en limitant les phases de surcharges de travail. La démarche participative déployée au sein de notre unité sera illustrée et les résultats des gains organisationnels seront présentés.
L’auteur déclare n’avoir aucun conflit d’intérêts potentiel par rapport à la recherche et n’a pas reçu de soutien financier.