Validation of a semi-automatic vacuum pack machine for batch preparations
7 October 2016
C. Dupire1, L. Sauvaget1, C. Gary1, V. Servant1, R. Legeron1,2, A. Berroneau1, D. Breilh1,2, S. Crauste-Manciet1,3 1 Pharmaceutical technology department, Bordeaux University Hospital, France2 Department of Pharmacokinetics, Groupe PK/PD, INSERM U1034 - Bordeaux University Hospital, France
3 Laboratoire ARNA, ChemBioPharm, U1212 INSERM - UMR 5320 CNRS Bordeaux University, France
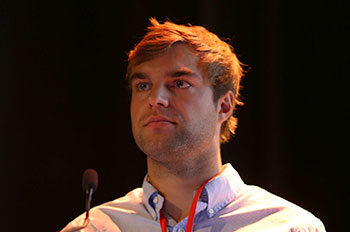
Introduction
To improve a quality approach of a production process whereas our workload increased, a part of our process is based on dose banding with batch production.
To preserve the sterility of the preparation we implemented a packaging under vacuum. The objective of this work was to validate the packaging method by assessing packaging integrity and risk of drug degradation.
Materials and Methods
For each volume of bag, three pressures and three durations of weld were tested with a semi-automatic vacuum pack machine C200 from MULTIVAC®. A total of 108 tests were performed, 3 different pressures were tested on 4 different volumes of Freeflex Fresenius® sodium chloride bags (50mL : 4, 8, 12 mBar – 100mL : 7, 11, 15 mBar – 250mL : 10, 15, 20 mBar – 500 mL : 20, 30, 40 mBar) at 3 different duration of seal (1.7, 2.3, 2,8 seconds). Each test was repeated 3 times. To identify the best condition of vacuum, the physical integrity of bags and seals were tested using colorimetric methods. A patent blue solution was injected in bag and the bag was then subjected to vacuum packaging. Packaging was removed and seal leaks were assessed by applying a pad on all seals and surfaces. The preservation of vacuum was assessed immediately after vacuum packaging and after one month by visual control and tightness test of the seals (ASTM F1929). Finally, due to the cooling effect of the vaccum packaging process we assessed the risk of precipitation on a model drug, undiluted 5 fluorouracil solution (50 mg/mL) by optical microscopy observation. 5 FU Final concentrations were also compared by HPLC before and after vaccuum packaging.
Results and discussion
Vacuum was achieved with the smallest remaining pressure inside bags (4mBar for 50mL, 7mBar for 100mL, 10mBar for 250mL and 20mBar for 500mL) and for a duration of sealing of 2.3 seconds. No leak of the bags was visually observed. No leak of the seals of the packaging was detected according to the ASTM test for one month.
With regards to 5 FU, no crystal was observed after vacuum packaging and no change in final concentration of the solution.
Conclusion
Vacuum packaging is an efficient and fast method to ensure containment of preparations during one month of storage. Besides physical parameters, lack of microbial ingress will complete our study.