Validation of a Rotary Vial washer for terminally sterilized product manufacture
2 October 2013
Andrew Sully, Catherine Talbot Cardiff and Vale University Health Board, SMPU,Cardiff, Wales, UK
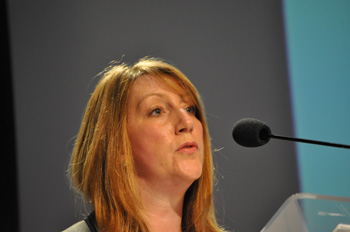
- The introduction of a new rotary vial washer used within the manufacture of terminally sterilised products required validation to ensure verification of performance. A protocol was derived to test the effectiveness of the machine as there were no published studies available.
- Chemical contamination, Endotoxin and Particulate removal studies revealed that the machine could remove residues and achieve particle removal in accordance with the Subvisible Particle test as defined in the British Pharmacopeia.
- Endotoxin Challenge tests confirmed a reported 3 log reduction in endotoxin in 10 and 100ml type 1 glass vials. Endotoxin levels were undetectable (<0.05EU/ml) in all samples washed prior to use.
Introduction
The introduction of a Penntech RW-500 rotary vial was to be employed to further automate terminal sterilisation manufacture. Validation was carried out in accordance with Annex 15 EU GMP. Performance qualification (PQ) was the responsibility of the Health Board and there were no published studies available to ensure effectiveness of the machine. Literature searches and discussion with MHRA GMP inspector derived a series of tests to demonstrate effective performance
Materials and Methods
10ml (Schott) and 100ml Type 1 Glass vials were containers used in the PQ study and washed in accordance with the parameters derived from the vial dryness test in the Operational Qualification. Samples under study were taken at the beginning and end of the wash cycle.
Chemical contamination tests
- Vials were prepared by the addition of 10ml of Riboflavin 0.02% w/v solution, agitated to ensure coverage and left to dry in an oven at 60C for 24hours. Washed vials were observed under UV light at 360nm for any signs of riboflavin contamination by appearance of fluorescence
Particulate challenge
- 0.25ml of Duke Particle standard (50µm) added to each vial and agitated to ensure even coverage, covered and dried at 60C until no visual water present. Spiked vials were washed and spiked vials and unspiked /unwashed vial were retained as controls.
- Endotoxin challenge vials were prepared using a final concentration of approximately 100EU/ml of Endotoxin Control Standard (Charles River), vortexed and dried in a vacuum oven at 60C and 25mmHg until no visual water detected. Spiked vials were washed and unwashed spiked vial (control) were tested using the Endosafe PTS system with the addition of 1ml of LAL reagent water and vortexed.
Results and Discussion
Chemical contamination studies revealed no fluorescence in any vial under UV light (360nm) and effective residue removal. The level of contamination observed was much higher than a vial used in normal operation. Effective particulate removal was observed and compliant with the BP subvisible Particulate test as shown below (Table 1). Three log reduction in endotoxin was observed in both vial sizes.
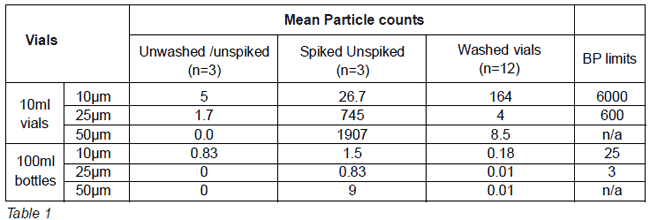
Conclusion
The machine was able to demonstrate verification of operation in worst case conditions. The washer was able to reduce endotoxin levels to undetectable limits and the use of depyrogenation processes for terminally sterilised manufacture was not justified on the basis of these results, pre-sterilisation bioburden and endotoxin testing in final product
Acknowledgments
The authors would like to thank Biopharma Process Systems and Penntech for their information and advice.
References
1. British Pharmacopoeia volume 1 (2011) Appendix XIII A. Particulate Contamination: Sub-visible Particles [online] available at http://www.pharmacopoeia.co.uk/bp2011/ixbin/bp.cgi?a=display&r=vIy5m38HLjz&n=9&id=928&tab=search. Last accessed 19.05.2011